A UK project aimed at recovering energy from waste exhaust heat could improve fuel consumption of internal combustion engines by 5%.
The initiative, which has £2 million of government funding, is called VIPER2 (Vehicle Integrated Powertrain Energy Recovery) and is led by Jaguar Land Rover. Other participants include Ford, European Thermodynamics and Nottingham University.
The target of the project is to recover a peak of 300 watts of electrical energy from a petrol engine being put through the World Harmonised Light Vehicle Test Procedure (WLTP) cycle. The recovered energy can then be used to drive the ancillaries or a hybrid motor. A key element of the project is a thermoelectric generator (TEG) mounted in the exhaust system downstream of the catalytic converter. Petrol engines convert only around 35% of the fuel they burn into mechanical energy. Most of the rest of the energy contained in the fuel is consumed by heat and frictional losses, while some of the energy contained in expanding hot exhaust gases is used to drive turbochargers or heat catalytic converters and particulate filters. The rest exits via the exhaust pipe or is absorbed by the car's cooling system and radiated to the atmosphere.
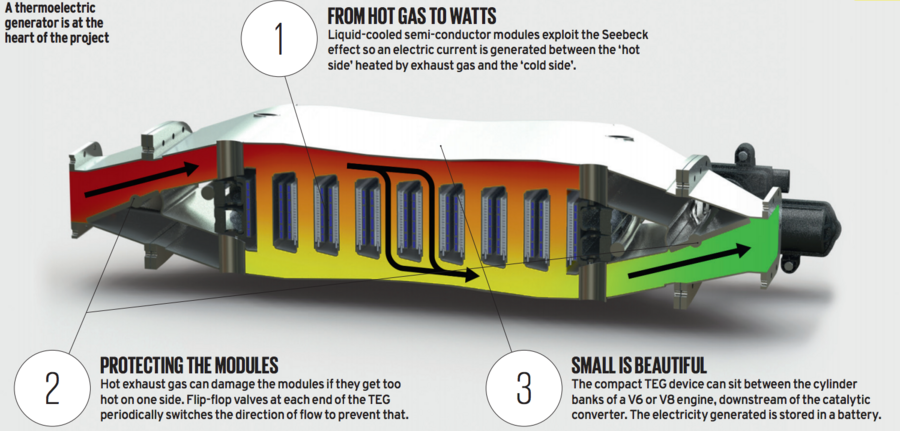
New engine valve tech gives petrols the efficiency of diesels
The exhaust gas leaving a catalytic converter is very hot. The TEG contains a number of thermoelectric modules, each one with a 'hot side' and a 'cold side.' The hot exhaust gas passes down one side of the TEG's gallery and can only exit the device by passing through the modules first.
Each module of the TEG also comprises two thermoelectric semiconductor materials, one positively and the other negatively charged. The device exploits 'the Seebeck effect'. When heat is applied at one end of a pair of semiconductors, the temperature difference between the hot and cold sides of the module generates a direct electric current.
The bigger the temperature difference between the two sides, the higher the current, so the modules are liquid cooled to maintain the difference. Because exhaust gas temperatures in petrol cars get so high, the TEG has a 'flip-flop valve' at each end to periodically switch the flow of the exhaust from one side to prevent the modules overheating. The valve can also bypass the TEG altogether.
The first TEG is installed in a vehicle for testing. Only one is needed per engine, regardless of whether it has an inline or vee cylinder configuration. "The design is modular so it can be made any length to suit the size of car. It could also fit into the vee of a V6 or V8," said JLR's Bob Gilchrist, who heads the project. Paul Chandler, a senior engineer on VIPER2, added: "It's still only a research idea and the first stage is to prove that it works." The concept could be ready for production by 2025.
Other heat energy recovery systems
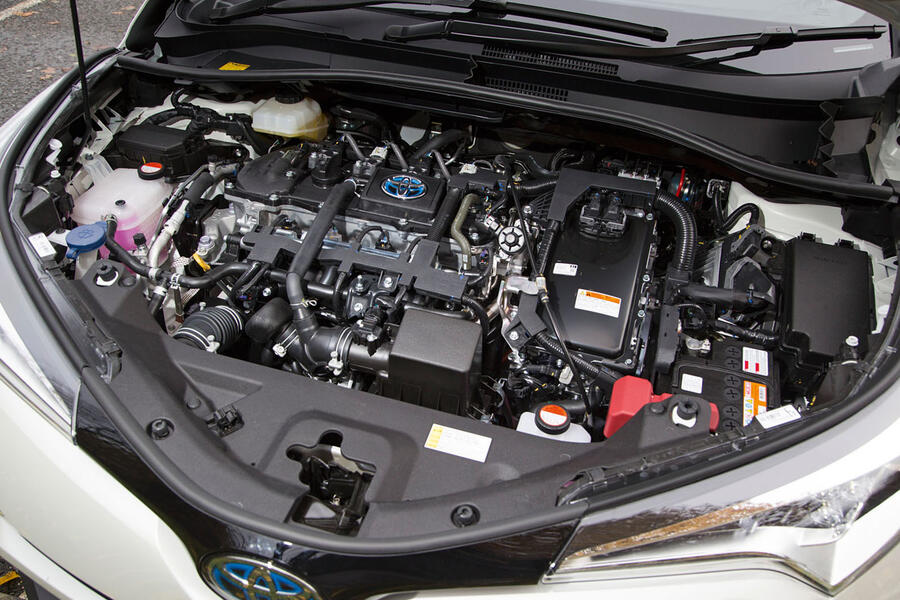
The thermoelectric generator being trialled by VIPER2 isn't the only heat energy recovery system.
Organic Rankine Cycle systems (ORC) vaporise an organic fluid below the boiling point of water, producing pressure to generate power using a turbine, for example.
The Toyota C-HR's engine (above) has an exhaust heat recovery system (EHRS) that raises the engine cooling system temperature more quickly from cold to improve engine efficiency.
Stirling engines, which produce power by exploiting the temperature difference between hot and cold gases, are also being looked at as a way to recover waste heat energy. All of these concepts were discovered more than 100 years ago.
Related stories:
Jaguar I-Pace development on course for March 2018 launch
Insight: Why Mazda has pursued 'dream' petrol engine technology
Jaguar I-Pace: first drive of electric SUV concept